![]() |
![]() |
Here is an explanation of ATEX and IECEx standards, markings, classification, directive and different zones.
ATEX products are differentiated from standard products by their markings, most noticeably the recognised Ex symbol.
Under the ATEX and IECEx schemes, products are classified and marked to show the areas in which they can be used, and the level of protection employed.
Straightpoint Ex products classifications:
ATEX – II 1 G
IECEx – ia IIC T4 Ga
Example:
For Straightpoint, current ATEX/IECEx equipment markings the protection concepts are:
ATEX – II 1 G where: Equipment Group II is for use in all other areas other than mines.
Category 1 for use Zones 0, 1 and 2 for gases/vapours.
Environment G for use in hazardous gas, vapour or mist environments.
IECEx – ia IIC T4 Ga
Type of Protection ia is Intrinsic Safety.
Gas Group IIC is gas, vapour or mist, except in coal mines.
Temperature Class T4 is up to 1350C (2480F)
Equipment Protection Level Ga – suitable for use in Zones 0, 1, 2.
Actual Straightpoint markings form part of the labels affixed to the ATEX/IECEx wireless loadcell products and held hand display unit.
In the European Union (EU) and the USA, all electrical/electronic or mechanical equipment used in explosive, or
potentially explosive atmospheres, must be manufactured to strict standards to ensure that the possibility of the equipment to cause an explosion, in both normal and abnormal operation, is minimised. This includes equipment being designed with appropriate safety devices and protection systems and being manufactured and tested under
controlled conditions. Compliance has to be verified by recognised third party professional bodies.
In the EU, the ATEX Directive defines technical and management systems requirements for compliance. In the USA and other international regions, similar requirements are specified by the IECEx scheme.
There is an accelerating growth rate for ATEX/IECEx approvals, principally driven by the upward demand for energy and growth amongst developing and emerging economies, and their increased awareness of the need for “Proof of compliance” with minimum safety standards.
Explosive Atmospheres
Under ATEX and IECEx, an explosive atmosphere is defined as a mixture of dangerous substances with air, under
atmospheric conditions, in the form of gases, vapours, mist or dust in which, after ignition has occurred, combustion
spreads to the entire unburned mixture.
Atmospheric conditions are commonly referred to as ambient temperatures and pressures. That is to say
temperatures of –20°C to 40°C and pressures of 0.8 to 1.1 bar.
Potentially explosive atmospheres can typically be found in industry sectors as:
- Onshore and offshore oil and gas rigs
- Petrochemical refineries
- Fuel distribution depots
- Oil and gas pipeline installation, repair and maintenance
- Chemical and pharmaceutical industry
- Mining
- Building, construction and civil engineering in hazardous environments
- Producers and users of solvents, paints, varnishes and other flammable liquids
- Printing and textiles
- Food manufacturers, wood processors, grain handling & storage - where dust is created
- Engineering where dust is created from machining, grinding and sanding
Organisations that operate within these and other industry sectors are obliged to assess their business activities to identify potential explosive atmospheres and to implement control measures to reduce the possibility of inadvertent explosion. Measures include using only Ex approved equipment. In the EU, this is a legal obligation.
The ATEX 2014/34/EU Directive
Also known as ATEX 95 and commonly referred to as the Equipment Directive.
The aim of the Directive (previously 94/9/EC) is to allow the free trade of 'ATEX' equipment and protective systems within the EU by removing the need for separate testing and documentation for each Member State.
It applies to both electrical and non-electrical equipment for use in potentially explosive atmospheres, which may be gas, mist, vapour or dust, above or below ground.
The directive defines essential health and safety requirements (EHSR) that need to be achieved by the manufacturer of the equipment. This usually involves testing and certification (ATEX EC-Type and/or IECEx Certificate of Conformity) by a 'third-party' certification body (known as a Notified Body) but manufacturers/suppliers can 'self-certify' equipment intended to be used in less hazardous explosive atmospheres (Category 3).
Certification ensures that the equipment or protective system is fit for its intended purpose and that adequate information is supplied with it to ensure that it can be used safely.
The directive requires that the equipment is marked to show equipment complies with the ATEX directive.
The directive also introduces categories of protection, which can be related to the zones classified by the workplace ATEX directive.
IECEx
IECEx is the International Electrotechnical Commission Scheme for Certification to Standards Relating to Equipment for Use in Explosive Atmospheres.
ATEX is driven by EU law whereas IECEx is a voluntary certification scheme. Both, however, provide an accepted means of proving compliance with IEC standards.
The difference between ATEX and IECEx is initially that ATEX is only valid in the EU and IECEx accepted globally.
Technical Standards
Both ATEX and IECEx both require compliance with the same technical standards, so in terms of technical content, there is basically no difference. The only visible difference is in many cases the marking on the device.
IEC (The International Electrotechnical Commission) Standard IEC 60079 is a suite of Standards that cover a wide standards relating to different types of equipment and protection measures in explosive atmospheres.
The applicable technical standards within this suite for Straightpoint ATEX/IECex products are:
IEC 60079-0 Explosive Atmospheres - Part 0: Equipment - General Requirements
This Standard specifies the general requirements for construction, testing and marking of electrical equipment and Ex Components intended for use in explosive atmospheres
IEC 60079-0 Explosive Atmospheres - Part 11: Equipment by Intrinsic Safety
This Standard specifies the construction and testing of intrinsically safe apparatus intended for use in an explosive atmosphere and for associated apparatus, which is intended for connection to intrinsically safe circuits which enter such atmospheres. This type of protection is applicable to electrical equipment in which the electrical circuits themselves are incapable of causing an explosion in the surrounding explosive atmospheres
IEC 60079-0 Explosive Atmospheres - Part 25: Intrinsically safe Electrical Systems
This Standard contains the specific requirements for construction and assessment of intrinsically safe electrical systems, type of protection "i", intended for use, as a whole or in part, in locations in which the use of Group I, II or III apparatus is required. This standard supplements and modifies the general requirements of IEC 60079-0 and the intrinsic safety standard IEC 60079-11
“Intrinsic Safety” is a protection technique applied to electrical equipment and wiring for hazardous locations. The technique is based on limiting electrical and thermal energy to a level below that which can cause ignition of a specific hazardous atmospheric mixture
Straightpoint ATEX/IECEx Lifting Equipment designed for lifting in hazardous areas
Ex Dynamometer load cell products available:
Radiolink plus | Wireless Loadpin | Wireless Compression | Wireless Shackle | Running Line Tensiometer
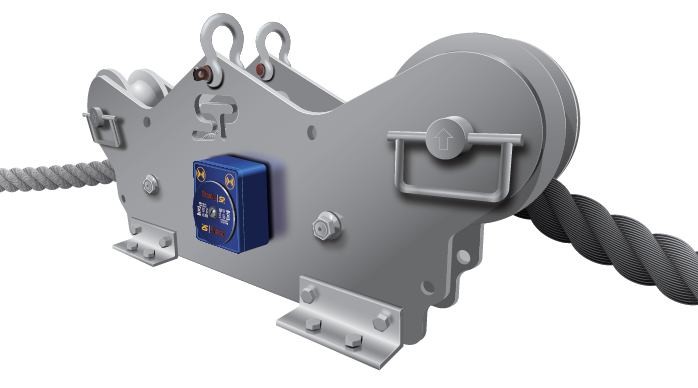
![]() |
![]() |
Need a price? Contact our team
The TIMH range is a Running Line Tensiometer or RLTM built with dockside, marine, offshore, towage and salvage applications in mind. Available with ATEX and IECEx approved to Ex ia II T4 Ga for use in zones 0, 1 and 2 hazardous environments (gas) and is designed for wire rope tension monitoring in applications with challenging hazardous areas.
All capacities in stock. It is particularly useful where there is no anchor or dead end on the line to rig a Straightpoint Radiolink-ATEX digital dynamometer to measure tension force. The TIMH is constructed from marine grade stainless steel and is suitable for many wire rope configurations up to 80t and will, as an option, calculate lineout in metres or feet along with line speed. The TIMH has several mounting points featured in its unique design but if other mounting options are required Straightpoint can provide a custom-engineered solution specific to your application.
Load data is transmitted wirelessly utilising the latest in IEEE 802.15.4 (2.4 GHz) technology providing safe, high integrity, error-free transmission of both static weight and dynamic load to our SW-HHP-ATEX handheld controller for use in hazardous areas with a range of 500m or 1640ft.
The TIMH utilises easily sourced Energizer® Ultimate Lithium AA Batteries and features advanced circuitry designed to protect the unit from damage associated with incorrectly installed batteries. This advanced circuitry extends battery life and eliminates issues associated with rechargeable battery pack charging, failure and replacement.
- Approved for use in hazardous zones
- Fully constructed from corrosion-resistant stainless steel
- IP67/NEMA6 Loadpin
- Gravity catches fitted to top sheave pins make wire rope installation quick and simple
- Maintenance free heavy duty bearings
- Options for line out available
- Software available to data log and monitor analogue outputs
- Large range of capacities to 80t and wire rope diameters up to 52mm/2”
- Line in/out, distance and speed
- Maintenance free heavy duty needle bearings
- Five-wheel design improving accuracy
APPLICATIONS
- Hazardous areas
- Offshore oil and gas
- Chemical industries
- 2-year warranty
- Design validated by F.E.A.
- Independently approved by CSA
SUPPLIED WITH THE FOLLOWING AS STANDARD
- Proof test certificate
- Operator Manual
- Carry/Storage Crate
Specifications/Technical Data
Wireless Approvals
Federal Communications Commission
FCC: W70MRF24J40MDME
Industry Canada
IC: 7693A-24J40MDME
Japan Certification
ID: 204-52-1
Part Number | TIMH10TR-ATEX | TIMH25TR-ATEX | TIMH56TR-ATEX | TIMH80TR-ATEX | TIMH150TR-ATEX |
Crosby Part number | 2789135 | 2789140 | 2789143 | 2789147 | 2789297 |
Capacity MET | 10 te | 25 te | 56 te | 80 te | 150 te |
Capacity IMP | 22,000 lb | 55,000 lb | 123,200 lb | 176,000 lb | 330,000 lb |
Resolution MET | 0.01 te | 0.02 te | 0.05 te | 0.1 te | 0.2 te |
Resolution IMP | 20 lb | 50 lb | 100 lb | 200 lb | 500 lb |
Wire rope Ø mm MET | 13-19 mm | 16-26 mm | 28-38 mm | 40-52 mm | 52-89 mm |
Wire rope Ø mm IMP | 1/2 in - 3/4 in | 5/8 in - 1 in | 1 1/8 in - 1 1/2 in | 1 5/8 in - 2 in | 2 in - 3 1/2 in |
Weight MET | 91 kg | 87 kg | 82 kg | 77 kg | 231 kg |
Weight IMP | 200.6 lb | 191.8 lb | 180.8 lb | 169.8 lb | 509.3 lb |
Approval Spec | Ex ia II C T4 Ga for use in zone 2, 1, and 0 - certificate number IECEx SIR 16.0041X & SIRA 16ATEX2108X | ||||
Battery Type | 4 x Energizer® Ultimate Lithium AA | ||||
Battery Life | 1200 hrs | ||||
Operating Temp MET | -10 to +50 °C | ||||
Operating Temp IMP | 14 to 122 °F | ||||
Accuracy | 2% FS | ||||
Range MET | Wireless version 500 m | ||||
Range IMP | Wireless version 1640 ft | ||||
Protection MET | IP67/NEMA6 | ||||
Max Speed MET | 20 m per minute | ||||
Max Speed IMP | 65 ft per minute | ||||
Line out and speed | Not available for ATEX | ||||
Dimension A MET | 865 mm | 865 mm | 865 mm | 865 mm | 1250 mm |
Dimension A IMP | 34.05 in | 34.65 in | 34.65 in | 49.21 in | |
Dimension B MET | 674 mm | 674 mm | 674 mm | 674 mm | 1050 mm |
Dimension B IMP | 26.53 in | 26.53 in | 26.53 in | 26.53 in | 41.33 in |
Dimension C MET | 324 mm | 324 mm | 324 mm | 324 mm | 416 mm |
Dimension C IMP | 12.75 in | 12.75 in | 12.75 in | 12.75 in | 16.37 in |
Dimension D MET | 111 mm | 111 mm | 111 mm | 111 mm | 153 mm |
Dimension D IMP | 4.37 in | 4.37 in | 4.37 in | 4.37 in | 6.02 in |
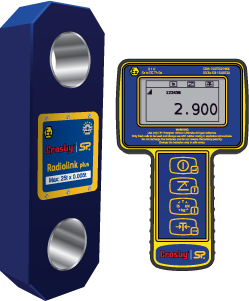
![]() |
![]() |
![]() |
Need a price? Contact our team
Dynamometer load cell approved to Ex ia II C T4 Ga for use in zone 0,1 & 2 hazardous areas. This intrinsically safe version of the bestselling Radiolink plus is capable of both weighing and dynamic load monitoring in hazardous environments such as on and offshore oil, gas and chemical industries. Available from stock in capacities from 1t to 300t, constructed from high-quality aircraft-grade aluminium and featuring an advanced internal design structure.
Paired with the SP Ex Handheld you can read up to four SP Ex load cells simultaneously allowing the operator to monitor a multi pick point lift from a single handheld at safe distances of up to 500m/1640ft with the added benefits of on-screen overload and calibration due warnings.
This internal design structure not only provides the product with an unrivalled strength to weight ratio but also allows the use of a separate internal sealed enclosure providing the load cell's electronic components with IP67/NEMA6 environmental protection even with the battery cover plate missing, making this industry-leading dynamometer even more suitable for use in the harshest environments. Featuring industry-leading wireless technology and range, the versatile Radiolink plus - ATEX is supplied with an update rate of 3Hz and can be easily configured to run at industry-leading speeds of up to 200Hz.
Data is transmitted wirelessly utilising the latest in IEEE 802.15.4 (2.4 GHz) technology providing safe, high integrity, error-free transmission of both static weight and dynamic load to an approved wireless handheld controller, the SW-HHP- ATEX includes an option to monitor four loadcells, simultaneously, allowing the operator to monitor a multi pick point lift from a single handheld.
The Radiolink plus- ATEX utilises easily sourced Energizer® Ultimate Lithium AA Batteries and features advanced circuitry designed to protect the load cell from damage if the batteries are incorrectly installed. This advanced circuitry extends battery life and the use of easily sourced batteries eliminates issues associated with rechargeable battery pack charging, failure and replacement.
It is easy to see why globally the Radiolink plus - is the number one choice for weighing and dynamic load monitoring in hazardous applications.
- Proprietary 2.4 GHz Wireless
- Industry-Leading Wireless Range
- Environmentally Sealed
- Unmatched Battery Life
- Internal Antennae
- Compact Size
- Remote On-Off
- LightweightPeak Hold
- Advanced Options Available
- Tare
- Zones 0,1&2 hazardous areas
- Error-free Data Transmission
- Unrivalled Resolution
APPLICATIONS
- Hazardous areas
- Offshore oil & gas
- Chemical industries
- 2 year warranty
- Design validated by F.E.A.
- DNV-GL Type Approval
- Independently approved by CSA
SUPPLIED WITH THE FOLLOWING AS STANDARD
- Proof test certificate
- Operator Manual
- Carry/Storage Case
- RFID Tagged
- Lithium AA Batteries
Specifications/Technical Data
![]() |
Ex battery type: SAFETY REMINDER |
![]() |
Ex Radiolink plus additional technical data
|
|
|
Wireless ApprovalsFederal Communications Commission
|
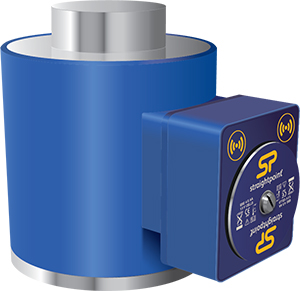
![]() |
![]() |
Need a price? Contact our team
LoadSafe - Wireless Compression Load Cell is available ATEX and IECEx approved to Ex ia II T4 Ga for use in zones 0, 1 and 2 hazardous environments (gas and is designed for the on and offshore oil and gas, chemical and other industries with challenging hazardous areas.
No longer hindered by troublesome and hard to maintain cables, large scale projects can be completed in a fraction of time previously required. Maintenance costs are all but eliminated due to the absence of cables and connectors, and the product's flexibility opens the door to a large number of applications in hazardous areas such as drilling platforms, silos and heavy lifting projects replacing unwieldy and inaccurate hydraulic loadcells previously used in similar applications.
SP's Wireless Compression Load Cells are machined from high-grade stainless steel, providing excellent strength and corrosion resistance. The heavy-duty, compact load cell utilises Straightpoint's advanced microprocessor based electronics and benefits from unrivalled resolution and accuracy. Data transmission is handled by the Straightpoint wireless systems proprietary transport protocol, is unmatched in performance and capable of a licence free transmission range of up to 500 metres or 1640 feet.
Load data is transmitted wirelessly utilising the latest in IEEE 802.15.4 (2.4 GHz) technology providing safe, high integrity, error-free transmission of both static weight and dynamic load to our SW-HHP-ATEX handheld controller for use in hazardous areas.
This latest range of compression loadcells utilise easily sourced Energizer® Ultimate Lithium AA Batteries and features advanced circuitry designed to protect the unit from damage associated with incorrectly installed batteries. This advanced circuitry extends battery life eliminates issues associated with rechargeable battery pack charging, failure and replacement.
- Approved for use in hazardous zones
- Proprietary 2.4 GHz Wireless
- Error-free data transmission
- No cable assemblies required
- Unrivalled resolution
- Unmatched battery life of 1200hrs
- Reduced maintenance cost
- Compact size
- Remote on-off
- Leading wireless range of 500m/1640ft
- Error-Free Data Transmission
- Internal antennae
- Hazardous areas
- Offshore oil and gas
- Chemical industries
- 2 year warranty
- Complies with ASME B30.26
- Design validated by F.E.A.
- Independently approved by CSA
SUPPLIED WITH THE FOLLOWING AS STANDARD
- Batteries
- Proof test certificate
- Operator Manual
- Carry/Storage Case
Specifications/Technical Data
![]() |
Ex battery type: SAFETY REMINDER |
![]() |
Compression load cell additional technical data
N.B. Clearance of box may vary from the images displayed depending on the capacity required. |
|
|
Wireless ApprovalsFederal Communications Commission
|
Part Number | WNI5TC-ATEX | WNI10TC-ATEX | WNI25TC-ATEX | WNI50TC-ATEX | WNI100TC-ATEX | WNI150TC-ATEX | WNI300TC-ATEX | WNI500TC-ATEX | WNI1000TC-ATEX |
Crosby Part number | 2789434 | 2789435 | 2789436 | 2789437 | 2789438 | 2789439 | 2789440 | 2789441 | |
Capacity MET | 5te | 10te | 25te | 50te | 100te | 150te | 300te | 500te | 1000te |
Capacity IMP | 11,000lb | 22,000lb | 55,000lb | 110,000lb | 220,000lb | 330,000lb | 660,000lb | 110,0000lb | 2200000lb |
Resolution MET | 0.001te | 0.002te | 0.005te | 0.01te | 0.05te | 0.05te | 0.1te | 0.2te | 0.5te |
Resolution IMP | 2lb | 5lb | 10lb | 20lb | 100lb | 100lb | 200lb | 500lb | 1000lb |
Units MET | tonne | tonne | tonne | tonne | tonne | tonne | tonne | tonne | tonne |
Units IMP | lb | lb | lb | lb | lb | lb | lb | lb | lb |
Weight MET | 7.2kg | 7.2kg | 7.2kg | 7.2kg | 16.5kg | 16.5kg | 66kg | 66kg | 173kg |
Weight IMP | 15.9lb | 15.9lb | 15.9lb | 15.9lb | 36.4lb | 36.4lb | 145.5lb | 145.5lb | 381.4lb |
Safety Factor | 3:1 | ||||||||
Approval Spec | Ex ia II C T4 Ga for use in zone 2, 1, and 0 - certificate number IECEx SIR 16.0041X & SIRA 16ATEX2108X | ||||||||
Battery Type | 4 x Energizer® Ultimate Lithium AA batteries | ||||||||
Battery Life | Loadcell 1200 hrs continuous | ||||||||
Operating Temp MET | -10 to +50 °C | ||||||||
Operating Temp IMP | 14 to 122˚F | ||||||||
Accuracy | +/- 0.1% FS | ||||||||
Frequency | 2.4GHz | ||||||||
Range | 500 metres | ||||||||
Range | 1640 feet | ||||||||
Data Rate | 3Hz (configurable to 200 Hz) | ||||||||
Protection | IP67 / NEMA6 | ||||||||
Dimension ØA MET | 100 | 100 | 100 | 100 | 152 | 152 | 185 | 185 | 362 |
Dimension ØA IMP | 3.94 | 3.94 | 3.94 | 5.98 | 5.98 | 7.28 | 7.28 | 14.25 | |
Dimension B MET | 127 | 127 | 127 | 127 | 184 | 184 | 300 | 300 | 310 |
Dimension B IMP | 5.00 | 5.00 | 5.00 | 5.00 | 7.24 | 7.24 | 11.81 | 11.81 | 12.20 |
Dimension ØD MET | 59 | 59 | 59 | 59 | 80 | 80 | 155 | 155 | 270 |
Dimension ØD IMP | 2.32 | 2.32 | 2.32 | 2.32 | 3.15 | 3.15 | 6.10 | 6.10 | 10.63 |
Dimension E MET | 16 | 16 | 16 | 16 | 26 | 26 | 27.5 | 27.5 | 40 |
Dimension E IMP | 0.63 | 0.63 | 0.63 | 0.63 | 1.02 | 1.02 | 1.08 | 1.08 | 1.57 |
Dimension F MET | M18 x 2.5 | M18 x 2.5 | M18 x 2.5 | M20 x 2.5 | M20 x 2.5 | M20 x 2.5 | M20 x 2.5 | M20 x 2.5 | M30x3.5 |
Dimension F IMP | M18 x 2.5 | M18 x 2.5 | M18 x 2.5 | M20 x 2.5 | M20 x 2.5 | M20 x 2.5 | M20 x 2.5 | M20 x 2.5 | M30x3.5 |
Dimension G MET | 152 | 152 | 152 | 152 | 432 | 432 | 432 | 432 | 950 |
Dimension G IMP | 5.98 | 5.98 | 5.98 | 5.98 | 17.01 | 17.01 | 17.01 | 17.01 | 37.40 |
Dimension H MET | 158 | 158 | 158 | 158 | 208 | 208 | 241 | 241 | 422 |
Dimension H IMP | 6.22 | 6.22 | 6.22 | 6.22 | 8.19 | 8.19 | 9.49 | 9.49 | 16.61 |
Dimension I MET | 6 | 6 | 6 | 6 | 7 | 7 | 21.5 | 21.5 | 102 |
Dimension I IMP | 0.23 | 0.23 | 0.23 | 0.23 | 0.27 | 0.27 | 0.27 | 0.54 | 4.02 |