News & Case Studies
- Details
- Written by Tanya
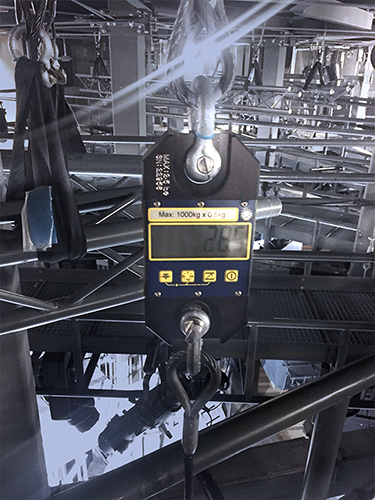
Straightpoint Load Cells Make Debut Performance at Rose Theatre Kingston
The Rose Theatre Kingston in South West London has added to its rigging inventory four 1t Loadlink Plus units from Straightpoint, which were most recently used during installation of sets for a production of Shakespeare’s King John. The famous play, directed by Trevor Nunn, was performed during a three-week run at the theatre. It required an elaborate set that included a large raised floor with an automated lift, two 9m-high towers and three platforms connected via numerous staircases and walkways. Any remaining empty space between those towers and walkways was finished with wooden cladding. Elsewhere on set, two large sliders concealed a throne.Wayne Parry, head of production at the Rose Theatre Kingston, explained that the load cells were used only for set installation, not during performances. He said: “Large steel sections were lifted using several motors (hoists) and, although the safe working load was well within the point capacity, we set the load cells to sound an alarm if any weight transfer came close to that capacity.”
The theatre will utilise the load cells for upcoming performances, including its next production—Good Canary, directed by John Malkovich, opens in mid-September—where three light-emitting diode (LED)-based video displays are the centrepiece to performances. The screens will be moved on tracks, while furniture moves on and off stage using floor tracks. The load cells will be used to monitor the loads distributed to the front of the overhead structure where the forces are greatest.
Parry explained that the theatre has a spider grid that houses the lighting rig and any performance-specific low load rigging. Most of the rigging is transferred to still sections in the roof that have a point load of 250kg. The stage dimensions beneath are 10m deep, 16m wide and 10m high.
He said: “The Rose grid is a complex affair and loads are spread between various sections to include the permanently installed bridges. As there is no flying system, the loads tend to be manageable as most of the work is fixed and much of it transfers through the stage floor. The stage floor itself is made up of steel deck rostras on steel legs.”
The Loadlink Plus units, manufactured from high-quality and high-tensile aircraft grade aluminum, were selected by Parry and his team in consultation with Straightpoint based on the theatre’s immediate requirements and flexibility for use in future shows.
Parry concluded: “Safety in any workplace is important and particularly so in the world of theatre, which compromises many different disciplines carried out simultaneously. Additionally, schedules are always tight and deadlines concrete, therefore, the need for clear and thorough safety procedures is vital.”
- Details
- Written by Tanya
Straightpoint Welcomes New York’s Electromatic as Distributor
Straightpoint has named Electromatic Equipment Co. Inc. a distributor of its force measurement, load monitoring and suspended weighing load cell equipment to the New York company’s diverse customer base.The partnership serves to complement Electromatic’s existing range of precision measuring instruments, which includes its own Checkline series of products, while contributing to Straightpoint’s ongoing expansion in North America, a region managing director David Ayling has slated for significant growth.
Ayling said: “Integral to achieving our goals is an effective distributor network and Electromatic are perfectly placed to redouble our efforts to grow in the regions and markets they represent. Every distributor partnership is different and in this case the breadth of our range is an appeal to a supplier that already carries an extensive portfolio of equipment, as our specialist equipment can provide measurement solutions that are not readily available elsewhere.”
Brett Linzer, chief technology officer, Electromatic Equipment, said: “Andrew Kaner [president] and I have noted the attention to detail in the Straightpoint product range. Some industrial products have the finish of a prototype, but Straighpoint products have the fit and finish of high-end consumer electronics—it’s obvious as soon as you open the box. They are intuitive, user friendly and, most importantly, they are dependable, even in the harshest of environments.”
Straightpoint has recently launched ATEX versions of its most popular product, the Radiolink plus wireless load cell, in addition to the wireless Handheld plus, compression cells, shackle cells, load pins and the Running Line Dynamometer (or TIMH).
Linzer anticipates high demand for these products in particular. He said: “Intrinsically safe, ATEX dynamometers to Zone 0, 1 and 2 classification are the first of their kind in this industry. Our customers will also note the TIMH running line tension meter, which is an ideal tool for measuring leader rope tension, while we also expect demand for the Radiolink plus, load shackles, compression load cells and load pins.”
Electromatic has customers in the lifting, shipping, aerospace, construction, military and mining industries, among others. In a recent visit to the Cedarhurst, New York facility, Linzer highlighted Ayling’s ability to apply the benefits of the Straightpoint range to applications in those sectors.
Linzer concluded: “We look forward to being a value-added representative for the Straightpoint brand by assisting users in finding the ideal lifting equipment for their application.”
Pictured above: Electromatic’s Andrew Kaner (left) and Brett Linzer with Straightpoint director David Ayling in New York.
- Details
- Written by Tanya
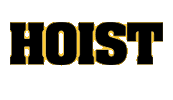
Critical mass
17 May 2016 Versabar Uses Straightpoint for 150 Ton Proof Load Test
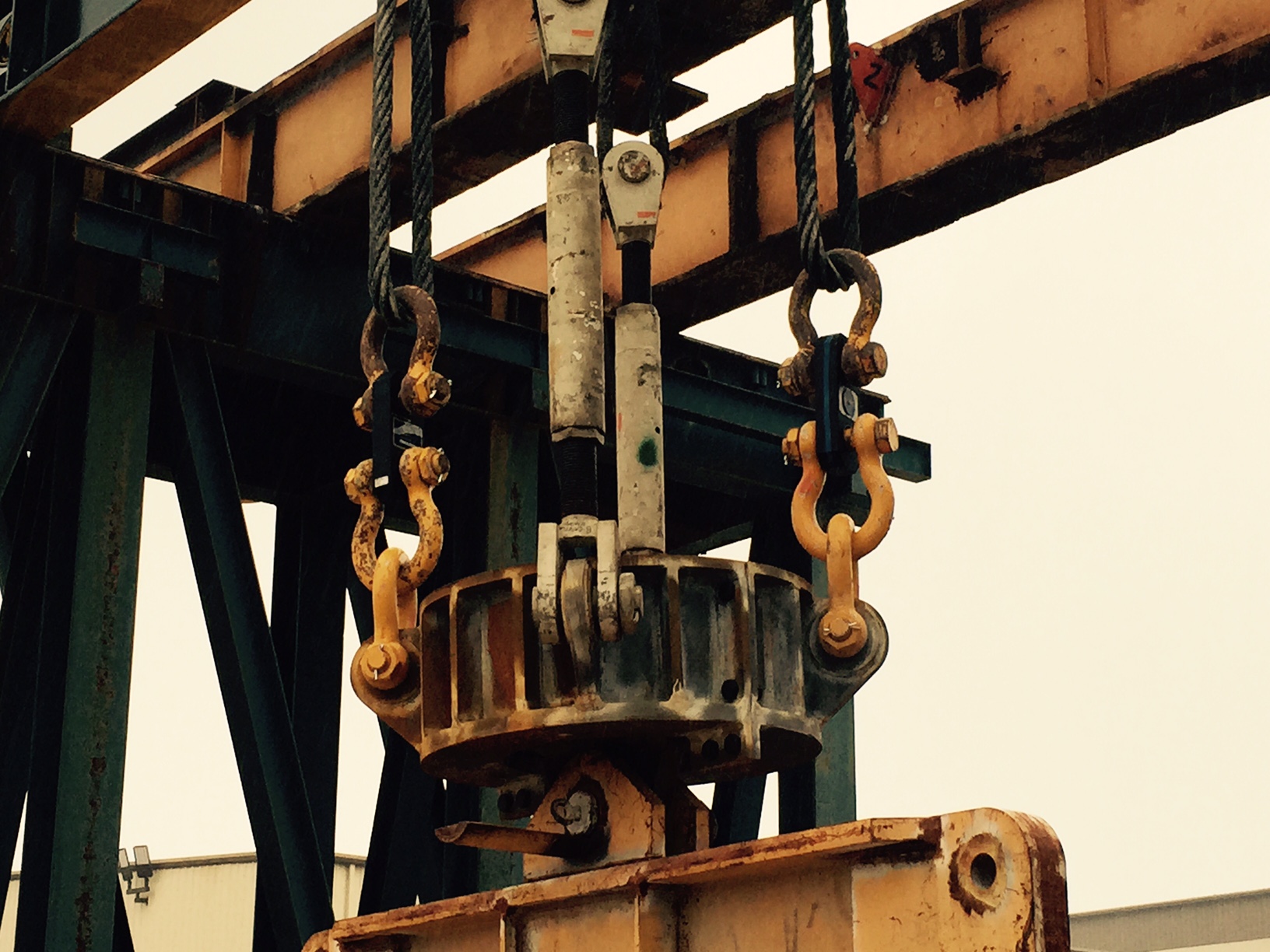
The component, owned by a Gulf of Mexico-based oil and gas company, was successfully tested by Versabar’s testing division, which uses load cells to determine applied load during system integration testing. In this case, setup and testing was completed in approximately 16 hours.
Tom Cheatum, sales and marketing director, Versabar, said: “One test is better than a thousand expert opinions and having accurate load monitoring is critical.”
Aaron Orsak, technical sales engineer, Straightpoint, said: “We have been building a relationship with Versabar over a couple of years and we are pleased that our initial dialogue has culminated in the supply of the RLP (Radiolink Plus) units from our U.S. stock for the well support clamp application.”
Orsak explained that the load cells were 50 ton capacity but they did not see the full 300,000 lb. load due to what he called the “mechanical advantage” included in the application on the test rig.
The Radiolink Plus, Straightpoint’s most popular product, is capable of both weighing and dynamic load monitoring at speeds up to 200Hz. It features high weatherproof protection to IP67 or NEMA 6, battery life of 1,200 hours and can be connected to the Straightpoint range of multi function handheld displays and data logging software.
Recently marking a year since joining the force measurement, load monitoring and suspended weighing load cell manufacturer, and formerly of Bishop Lifting Products Inc. and Certex USA, Houston-based Orsak is a trusted commentator on the state of the Gulf of Mexico market as it pertains to below-the-hook equipment.
He said: “The market has been reasonably depressed over the last six months, but things are on the uptick. Taking opportunities to be integrated into the marine construction industry is just one facet of a global plan to make the best of the economical environment, as credible sources continue to forecast an increase in offshore investment.”
- Details
- Written by Tanya
New Load Cell Test Facility at Straightpoint HQ
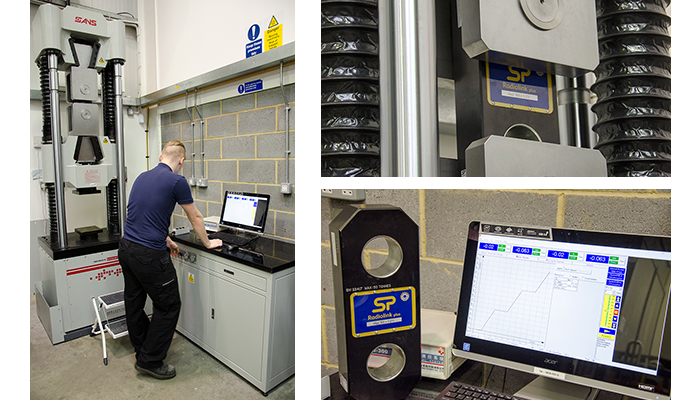
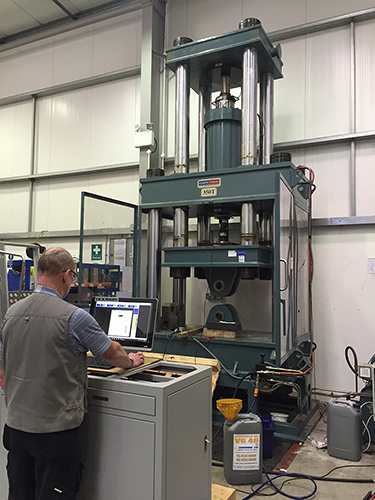
A state-of-the-art 100t universal test machine is the centrepiece of a new load cell testing facility at UK manufacturer Straightpoint’s headquarters in Hampshire.
The machine, manufactured by USA company MTS, can test in compression and tension, offering the ability to test Straightpoint’s entire range of load cells up to 100t.
Meanwhile, as part of ongoing investment in testing capability, a 10-year-old, 350t rig has been upgraded with new servo controls and software, while a 55t tension-only machine, also in situ, completes the range of testing equipment available to the company’s engineering team.
Alfie Lee, operations director, said: “Improving our test facility was a significant undertaking on two levels. First, the equipment and software represented a substantial economic investment and, second, it was a logistical challenge. We had to make room for installation of the new machine, while relocating other equipment all within a tight timeframe in a busy manufacturing environment alongside our production and testing schedule.”
The MTS universal test machine, which provides testing capability verified by a third-party UKAS laboratory, arrived in the UK at the turn of the year. Local supplier Rapid Response Solutions provided a mini crane and oversaw lifting and moving operations related to installation and relocation of equipment.
David Ayling, director, said: “The MTS unit is a universal testing machine combined with customised tooling, creating a top-of-the-range rig tailored to the specific requirements of force measurement, load monitoring and suspended weighing load cell equipment.”Straightpoint engineers refer to the rigs within the new test centre by codename and choose SP6 (the upgraded 350t rig), SP7 (55t) or SP14 (the new rig) depending on capacity and type of test they need to complete. Engineers, who previously applied loads and controlled operations manually, now have access to closed-loop, servo-controlled testing ability when using SP6 and SP14.
Lee added: “We can now programme test routines, which means when we need to proof test a load cell and take the force to 50t three times, our engineers don’t have to apply, un-apply and reapply the load manually. Our throughput has been dramatically increased as a result.”
In addition to calibration, the new machine will support Roshan Divakaran, design engineer, and his team in ongoing research and development programmes.
- Details
- Written by Tanya
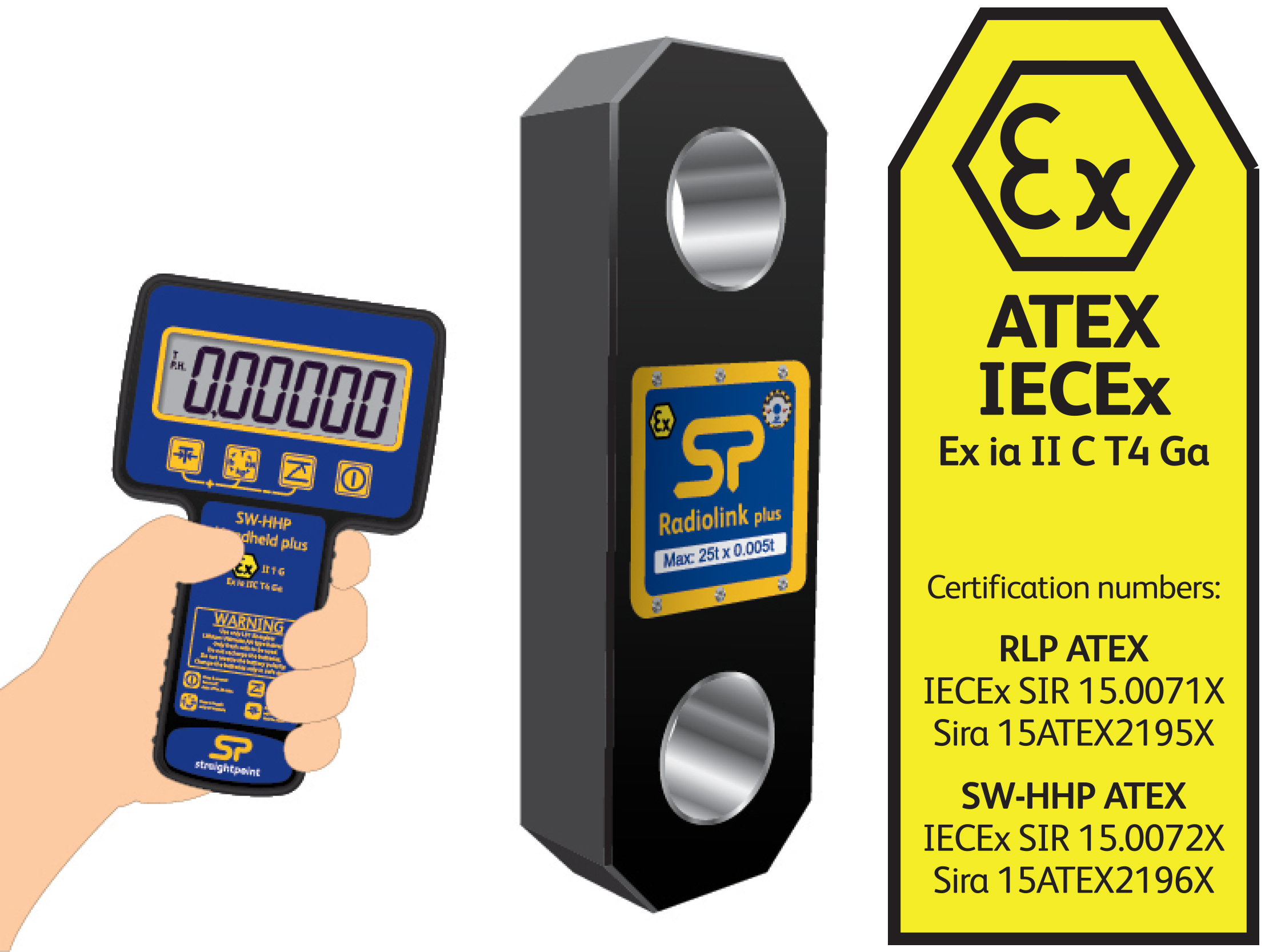
At the turn of the year, the force measurement, load monitoring and suspended weighing load cell equipment manufacturer launched an ATEX and IECEx version of its most popular product, the Radiolink Plus wireless load cell, which met Zone 0, 1 and 2 hazardous area classification.
An ATEX version of the wireless Handheld Plus followed, while other wireless products including compression cells, shackle cells, load pins and the Running Line Dynamometer (or TIMH), part of the manufacturer’s tension in motion range, are also in accordance with the new 2014/34/EU directive and boast classification in the three zone, including 0 (an area in which an explosive gas atmosphere is present continuously or for long periods)—unprecedented in wireless below-the-hook force measurement technology.
Roshan Divakaran, design engineer, Straightpoint, said: “We have been in close collaboration with the Sira Certification Service, an independent certification body, for more than two years and it has been very helpful with the new directive implementation and certifications for the new products we’ve introduced. We have not only expanded our ATEX range of products, but we will be in a position to supply them from the first week of May—almost simultaneous with the new directive becoming effective.”
Divakaran explained that the notable changes to the directive largely centre on terminology, citing references to an EU Declaration of Conformity rather than EC Declaration of Conformity, prevalent in 94/9/EC. He also pointed to the EC type examination certificate becoming an EU type examination certificate in 2014/34/EU.
David Ayling, director, Straightpoint, said: “We have come a long way since making a decision in early 2014 to introduce the benefits of our best selling product, the Radiolink Plus, to applications where products that meet the requirements of ATEX are required to work in extremely hazardous environments. To launch the expanded range as the 2014/34/EU directive becomes effective is testimony to the dedication of Roshan and his team in addition to the strength of our relationship with the Sira Certification Service.”
Divakaran said: “We are experiencing growing demand for the ATEX products and anticipate continued interest in the Radiolink Plus and the expanded range, heightened by 2014/34/EU becoming effective as we speak.”