All SP loadcells are strain gauged based and use the Wheatstone bridge principle. This article explores the science involved and how a load cell really works.
History
A load cell (or loadcell) is a transducer which converts force or mass into a measurable electrical output, most commonly stated as ## milli volt per volt (mV/V).
Although there are many varieties of force sensors such as hydraulic, piezo and pneumatic strain gauge based load cells are the most commonly used type.
In 1843, English physicist Sir Charles Wheatstone devised a bridge circuit that could measure electrical resistances. The Wheatstone bridge circuit is ideal for measuring the resistance changes that occur in strain gauges. Although the first bonded resistance wire strain gauge was developed in the 1940s, it was not until modern electronics caught up that the new technology became technically and economically feasible.
Wheatstone Bridge Circuit
The Science
SP Strain gauge loadcells convert the load acting on them into electrical signals. The gauges themselves are bonded onto the loadcell body in carefully calculated positions. When a force is applied the loadcell body deforms.
In most cases, four strain gauges are used to obtain maximum sensitivity and temperature compensation.
Strain gauge
Two of the gauges are usually in tension, and two in compression, and are wired with compensation adjustments to balance zero.
When a load is applied, the strain changes the electrical resistance of the gauges in proportion to the load – SP electronics then amplify and measure this change in proportion and convert it to a display in a known calibrated engineering unit such as tonne, pounds, KiloNewtons or Kilograms allowing the loadcell operator accurate and repeatable measurement.
Types of Load cell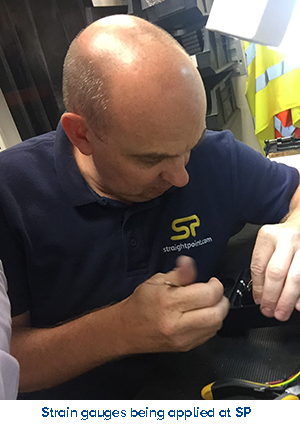
There are several common types of loadcell:
• Loadlink – a block of material with a loading hole for a shackle at each end allowing tensile forces to be applied
• Shear beam - a straight block of material fixed on one end and loaded on the other
• Double-ended shear beam, a straight block of material fixed at both ends and loaded in the centre
• Compression loadcell, a block of material designed to be loaded at one point or area in compression
• ‘S’ beam loadcell, a ‘S’ shaped block of material that can be used in both compression and tension (load links and tension load cells are designed for tension only)
• Shear Loadpin, a round loadcell that senses the force applied across it, via strain gauges installed within a small bore through the centre of the pin. Two grooves are machined into the outer circumference of the pin to define the shear planes.
Excitation and rated output
The Wheatstone bridge is excited with stabilized voltage (usually 3vdc with SP products but could be up to 20v).
The difference in voltage proportional to the load then appears on the signal outputs in mv/v.
A loadcell output is rated in millivolts per volt (mV/V) of the difference voltage at a fully rated mechanical load. So a 2 mV/V loadpin will provide a 6 millivolt signal at full load when excited with 3v.
Typical sensitivity values are 1 to 3 mV/V; most SP load cells are rated around 1.5mV/V.
Four & Six wire load cells
Some load cells have a cable with 4 wires and a screen; others have a cable with 6 wires and a screen. Those with 6 wires, in addition to the +input, -input, +signal and -signal terminations, have 2 wires called +Sense and -Sense. These are sometimes called +Reference (or +Ref) and -Reference (or -Ref).
The main difference in the function of these 2 types is that load cells with a 6-wire cable can compensate for variations in the actual excitation voltage they receive from the amplifier, indicator or PLC. The resistance of an electrical cable (conductor) varies according to its length and any temperature changes, resulting in variations in the excitation voltage at the load cells. With long cables, there will be a drop in voltage from the original value supplied by the amplifier, indicator or PLC and the advantage of a 6-wire load cell is that this drop in voltage can be quickly and effectively compensated without it affecting the load measurement.
4 wire load cells
4 wire load cells are already calibrated and thermally compensated together with the permanent length of cable supplied during their manufacture. SP recommend that you do not shorten the cable of a 4-wire load cell if it is too long; it is better to coil up excess cable. This is because the factory calibration and compensation of a 4-wire load cell will be compromised if you shorten the cable. There are no sense wires to compensate for the new cable length.
When connecting 4-wire load cells together into a junction box before the amplifier, indicator or PLC, we recommend using a dedicated 6-wire load cell cable to connect the junction box to the amplifier, indicator or PLC. This will compensate for any voltage drops over the length of the cable between them. In any event, the cable should be well shielded and have sufficient cross section (at least 0.2 mm sq) to limit the voltage drop along its length.
6 wire load cells
The above precaution about cutting the cables does not apply to load cells with a 6 wire cable. The two sense wires are capable of measuring the actual excitation voltage seen at the Wheatstone bridge inside the load cell, therefore the mV signal from the load cell can be adjusted according to the actual excitation it experiences. If an installation engineer wants to shorten the cables, they can do so without compromising the load cell performance.
Like to know more? Contact our team